HPEVS Frequently Asked Questions
Header Content Region
Insert text, image or banner ads here, or just delete this text and leave this area blank!
Mining Vehicle Systems
Specialty motors designed and built for your specific applications!
To get information, please click on "Details" tab below.
Specialty motors designed and built for your specific applications!
To get information, please click on "Details" tab below.
Utility Vehicle Systems
We have a drive system to fulfill your utility vehicle requirements!
To get information, please click on "Details" tab below.
We have a drive system to fulfill your utility vehicle requirements!
To get information, please click on "Details" tab below.
Diagnostic and Troubleshooting Documentation.
To obtain this information, please click on "Details" tab below.
To obtain this information, please click on "Details" tab below.
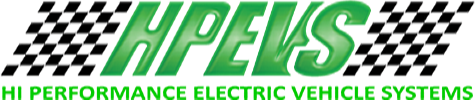
Innovation in Motion, Powered by Electricity
Newsletter Signup
Frequently Asked Questions
- The short answer is no. Our systems are designed to be used as a replacement of a vehicles original internal combustion engine, not as a supplement to an original EV, PZEV production vehicle design.
- HPEVS and Curtis DOES supply a Limited Warranty and the information contained about the warranty is contained within the .
- No, the controller will come to you already pre-programmed with the software that will be needed to run your vehicle. The system is basically a plug and play system.
- The number of lithium ion cells that can be used with our systems is limited by the Curtis controller. The controllers can only handle a certain amount of voltage and if the voltage exceeds that limit, the controller will go into a cutback situation. With that being said, the amount of lithium ion cells that can be used with the different controllers we sell are:
- 72 volt systems: 28 cells maximum
- 96 volts systems: 36 cells maximum
- 144 volt systems: 48 cells maximum
- An induction or asynchronous motor is a type of AC motor where power is supplied to the rotor by means of electromagnetic induction, rather than a commutator or slip rings as in other types of motor. A 3 phase induction motor has a simple design, inherently high starting torque, and high efficiency.
- An EV (electric vehicle) is a motor vehicle propelled exclusively by electricity. While generally used in reference to electric powered automobiles, a great many non-road going vehicles including forklifts, burden carriers, and golf carts are electric powered. As an extreme example even the Lunar Rover used by the astronauts on the moon would be considered an EV.
- Regen is short for regenerative braking. This basically is a system by which the energy of a decelerating EV is harnessed, either by using the drive motor as a generator, or by driving a separate generator. The electricity created by this process is fed back into the drive battery pack, restoring some of the charge. Regenerative braking seldom has a significant effect on overall range, but it does improve driveability, and reduces brake wear. Most AC drive electric vehicles include this feature, but it is only rarely found on DC drive EV's.
- We recommend using the GIGAVAC brand of contactors.
- Our standard systems that utilize an 48 VDC coil uses GIGAVAC part number GV200QA-1.
- Systems that we sell that utilize the "1239E" controllers will use an 12 VDC coil uses GIGAVAC part number GV200PA-1.
- Conversions have been done for less than 5000USD, but that is not the norm. As with many aspects of conversion, what you want from the vehicle affects the cost.
A high performance EV needs a controller that can put a lot of amps into the motor for high torque, and a high voltage battery pack for high speed. The need for high current leads to the selection of advanced AGM batteries, which in turn drives the requirement for sophisticated charging and battery balancing technology. Each of these selections drives up the cost.
An EV for everyday use runs the middle of the road. Depending once again on how many features are designed into it, these conversions can cost from 6000 to 10,000 not including the cost of the base vehicle.
- YES. The faster you go with a gas-powered vehicle, the more gas you will use. It’s the same with a battery-powered vehicle.
- You can find information on this website about what the flashing LED lights on the controller mean. Follow this to the pages containing information on how to read the flashing LED's and the corresponding error codes.
- More than likely the problem is with how the controller is programmed in relationship to the throttle type that you received. Unless otherwise specified, the controller will be programmed for a throttle type 3, 2-wire, 0-5K ohm potentiometer such as the Curtis PB-6. This only pertains to auto and motorcycle conversions.
- The information can be found many different ways. Below is the link that you can follow:
- They can also be found on the home page located in the center news box:
- Lastly, you can also surf to the instructions by way of the drop down menu "The Drive Systems" located on the top menu bar or on the Main Menu bar located on the left side of all HPEVS web pages. Find the link towards the bottom called "Power Graphs for Motors" and hover over this link, then hover over the sub-menu called "Power Graphs" and select the motor that is of interest.
- This information can be found many different ways. Below are direct links to the PDF's that contain the information:
- You can find the links on the home page located within the right side news box called Schematics, Instructions and Troubleshooting:
- Lastly, you can also surf to the instructions by way of the drop down menu "The Drive Systems"located on the top menu bar or on the Main Menu bar located on the left side of all HPEVS web pages. Then surf down to "Instructions" at the bottom of the list, and finally click on the link "Software Programming Instructions".
- There are a few ways that you can obtain the electrical schematics for the system that you are using. You can find the links on the home page located on the right side news box called "Schematics, Instructions and Troubleshooting:
- Lastly, you can also surf to the instructions by way of the drop down menu "The Drive Systems" located on the top menu bar or on the Main Menu bar located on the left side of all HPEVS web pages. Then surf down to "Electrical Schematics" near the bottom of the list, and finally click on the link of interest to obtain the electrical schematic for your needs.
- There are a few places that the software package information is located:
- There are labels that are affixed to the packages that were shipped.
- One label is attached to the cardboard sleeve that the controller was located within.
- Another label will be attached to the cardboard box that contains the controller.
- Another possible location will be on the box that the motor is packaged in.
- If the system is up and running, you can obtain the information through the Curtis 840 Spyglass display that comes with the HPEVS system. You will need to enter in "Diagnose" mode to obtain this information. Certain software packages allow for this feature.
- If you have a Curtis handheld programmer or own the Curtis 1314 programming station, you can retrieve the information as well.
- There are labels that are affixed to the packages that were shipped.
- The way the the software version information is written like this example (12.109.511) and is read from left to right. The first value prior to the first period is the OS (Operating System). The middle value prior to the next period is the build number. The last digits are the application version.
- If you call into us and are needing some assistance with your system, please have this information readily available so we can better assist you.
The following set-up parameters are the target frequency levels based on the number of cylinders of the original engine:
- 4 cylinder engine = 266 Hz (Default setting)
- 6 cylinder engine = 400 Hz
- 8 cylinder engine = 532 Hz
NOTE: This set-up will only work for digitally controlled tachometers and may or may not work with tachometers that use pulses from a distributor. Optional Isolation module required. .
Copyright 2012-2024. Hi Performance Electric Vehicle Systems. All Rights Reserved.